Calibração: Como Garantir a Precisão e a Confiabilidade dos Seus Equipamentos
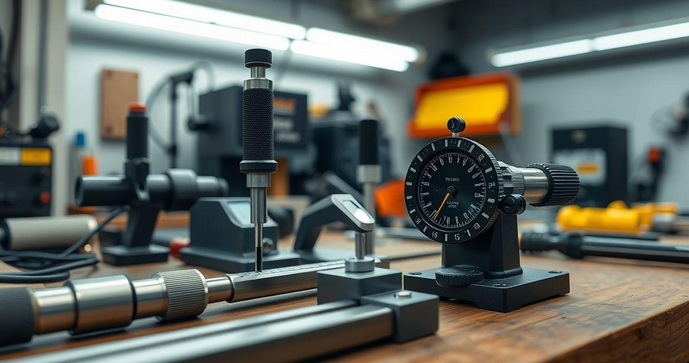
Por: Guilherme - 28 de Março de 2025
A calibração é um processo fundamental para garantir a precisão e a confiabilidade dos equipamentos utilizados em diversas áreas, como indústria, laboratórios e serviços técnicos. Ao realizar a calibração de forma adequada, é possível evitar erros que podem comprometer a qualidade dos resultados e a segurança das operações. Neste artigo, abordaremos a importância da calibração, os passos necessários para realizá-la corretamente, os erros comuns a serem evitados e a frequência ideal para manter seus equipamentos sempre em conformidade.
Importância da Calibração para Equipamentos Precisos
A calibração é um procedimento essencial que assegura que os equipamentos de medição e controle operem com precisão e confiabilidade. Em diversas indústrias, a precisão das medições é crucial para garantir a qualidade dos produtos e a segurança dos processos. A calibração envolve a comparação de um instrumento de medição com um padrão conhecido, permitindo ajustes que garantam que as medições estejam dentro das especificações desejadas.
Um dos principais motivos para a calibração é a manutenção da qualidade. Em setores como o farmacêutico, alimentício e de saúde, a precisão das medições pode impactar diretamente a segurança do consumidor. Por exemplo, em um laboratório, a calibração de balanças e pipetas é vital para garantir que as dosagens de medicamentos sejam exatas. Qualquer erro pode resultar em consequências graves, como a administração de doses inadequadas que podem comprometer a saúde dos pacientes.
Além disso, a calibração é fundamental para a conformidade com normas e regulamentos. Muitas indústrias são obrigadas a seguir padrões rigorosos de qualidade, como as normas ISO. A calibração regular dos equipamentos é uma exigência para manter a certificação e garantir que os processos atendam aos requisitos legais. A falta de calibração pode resultar em não conformidades, que podem levar a multas, sanções e até mesmo à suspensão das operações.
Outro aspecto importante da calibração é a redução de custos. Equipamentos que não estão calibrados corretamente podem levar a medições imprecisas, resultando em desperdício de materiais e tempo. Por exemplo, em uma linha de produção, um sensor de temperatura que não está calibrado pode causar o superaquecimento de um produto, levando à necessidade de descarte e retrabalho. Ao garantir que os equipamentos estejam calibrados, as empresas podem minimizar esses riscos e otimizar seus processos.
A calibração também contribui para a segurança operacional. Em ambientes industriais, equipamentos mal calibrados podem representar riscos significativos. Por exemplo, em uma autoclave, a calibração dos sensores de temperatura e pressão é crucial para garantir que os ciclos de esterilização sejam eficazes. A falta de calibração pode resultar em falhas na esterilização, colocando em risco a saúde dos pacientes e a integridade dos instrumentos médicos. Portanto, a Manutenção de autoclave deve incluir a calibração regular para garantir a segurança e a eficácia dos procedimentos.
Além disso, a calibração é um investimento na durabilidade dos equipamentos. Instrumentos que são calibrados regularmente tendem a ter uma vida útil mais longa. Isso ocorre porque a calibração ajuda a identificar problemas antes que se tornem sérios, permitindo que as empresas realizem manutenções preventivas e evitem falhas catastróficas. Ao prolongar a vida útil dos equipamentos, as empresas podem economizar significativamente em custos de substituição e reparo.
Por fim, a calibração é um componente essencial da cultura de qualidade dentro de uma organização. Ao promover a importância da calibração entre os funcionários, as empresas podem criar um ambiente de trabalho que valoriza a precisão e a qualidade. Isso não apenas melhora a moral da equipe, mas também resulta em produtos e serviços de maior qualidade, aumentando a satisfação do cliente e a reputação da empresa no mercado.
Em resumo, a calibração é vital para garantir a precisão e a confiabilidade dos equipamentos em diversas indústrias. Ela assegura a qualidade dos produtos, a conformidade com normas e regulamentos, a redução de custos, a segurança operacional e a durabilidade dos equipamentos. Investir em calibração não é apenas uma questão de conformidade, mas uma estratégia inteligente para otimizar processos e garantir a satisfação do cliente. Portanto, as empresas devem priorizar a calibração regular de seus equipamentos como parte de suas práticas de manutenção e gestão da qualidade.
Passo a Passo para Realizar a Calibração
A calibração é um processo sistemático que garante que os instrumentos de medição estejam funcionando corretamente e fornecendo resultados precisos. Realizar a calibração de forma adequada é essencial para manter a qualidade e a confiabilidade dos dados coletados. A seguir, apresentamos um passo a passo detalhado para realizar a calibração de equipamentos, garantindo que você siga as melhores práticas.
1. Preparação e Planejamento
Antes de iniciar o processo de calibração, é fundamental realizar um planejamento adequado. Isso inclui a identificação do equipamento que será calibrado, a definição dos padrões de referência que serão utilizados e a coleta de todos os materiais necessários. Verifique se você possui os instrumentos de calibração apropriados, como padrões de referência, ferramentas e manuais do fabricante.
2. Verificação do Equipamento
Antes de iniciar a calibração, é importante verificar o estado geral do equipamento. Inspecione visualmente o instrumento em busca de danos, sujeira ou desgaste. Certifique-se de que todas as partes móveis estão funcionando corretamente e que não há obstruções que possam afetar a medição. Caso o equipamento apresente problemas, é recomendável realizar reparos antes de prosseguir com a calibração.
3. Estabelecimento de Condições Ambientais
A calibração deve ser realizada em condições ambientais controladas. Fatores como temperatura, umidade e pressão atmosférica podem influenciar as medições. Portanto, é importante garantir que o ambiente esteja dentro das especificações recomendadas pelo fabricante do equipamento. Utilize termômetros e higrômetros para monitorar as condições ambientais durante o processo de calibração.
4. Realização da Calibração
Com o equipamento preparado e as condições ambientais adequadas, você pode iniciar o processo de calibração. Siga as instruções do fabricante para realizar a calibração corretamente. Isso geralmente envolve a comparação das medições do instrumento com os padrões de referência. Registre as leituras em um formulário de calibração, anotando as discrepâncias encontradas.
Se o equipamento não estiver dentro das especificações, ajuste-o conforme necessário. Isso pode incluir a realização de ajustes mecânicos ou eletrônicos, dependendo do tipo de instrumento. Após realizar os ajustes, repita as medições para garantir que o equipamento esteja agora calibrado corretamente.
5. Documentação dos Resultados
Após concluir a calibração, é essencial documentar todos os resultados. Isso inclui as medições iniciais, os ajustes realizados e as medições finais. A documentação deve ser clara e precisa, permitindo que outros profissionais possam entender o processo realizado. Além disso, mantenha registros de calibração para futuras referências e auditorias.
6. Manutenção e Recalibração
A calibração não é um processo único; é uma prática contínua. Após a calibração inicial, é importante estabelecer um cronograma de manutenção e recalibração. A frequência da recalibração pode variar dependendo do tipo de equipamento e da intensidade de uso. Equipamentos que são utilizados com frequência ou que estão sujeitos a condições adversas podem exigir calibrações mais frequentes.
Além disso, a Manutenção autoclave deve incluir a calibração regular dos instrumentos utilizados para garantir a eficácia dos processos de esterilização. Isso é crucial para a segurança dos pacientes e a conformidade com as normas de saúde.
7. Treinamento da Equipe
Por fim, é fundamental que a equipe responsável pela calibração esteja devidamente treinada. O conhecimento sobre os procedimentos corretos de calibração, as especificações dos equipamentos e a interpretação dos resultados é essencial para garantir a precisão das medições. Realizar treinamentos regulares e atualizações sobre novas tecnologias e métodos de calibração pode melhorar significativamente a qualidade do trabalho realizado.
Em resumo, a calibração é um processo crítico que deve ser realizado com atenção e rigor. Seguir este passo a passo garantirá que seus equipamentos estejam sempre funcionando corretamente, proporcionando medições precisas e confiáveis. A manutenção regular e a documentação adequada são essenciais para manter a qualidade e a conformidade com as normas, assegurando a segurança e a eficácia dos processos em sua organização.
Erros Comuns na Calibração e Como Evitá-los
A calibração é um processo crítico para garantir a precisão e a confiabilidade dos instrumentos de medição. No entanto, existem diversos erros que podem ocorrer durante esse procedimento, comprometendo os resultados e a eficácia dos equipamentos. Neste artigo, abordaremos os erros mais comuns na calibração e como evitá-los, assegurando que seus instrumentos funcionem corretamente e atendam às especificações necessárias.
1. Falta de Planejamento Adequado
Um dos erros mais frequentes na calibração é a falta de um planejamento adequado. Muitas vezes, os profissionais iniciam o processo sem uma compreensão clara dos requisitos do equipamento ou das condições ambientais necessárias. Para evitar esse erro, é fundamental elaborar um plano detalhado que inclua a identificação do equipamento, os padrões de referência a serem utilizados e as condições ideais para a calibração. Além disso, é importante garantir que todos os materiais e ferramentas necessárias estejam disponíveis antes de iniciar o processo.
2. Ignorar as Condições Ambientais
As condições ambientais, como temperatura e umidade, podem afetar significativamente os resultados da calibração. Um erro comum é realizar a calibração em ambientes que não atendem às especificações recomendadas pelo fabricante. Para evitar esse problema, sempre verifique as condições ambientais antes de iniciar a calibração. Utilize termômetros e higrômetros para monitorar a temperatura e a umidade, garantindo que estejam dentro dos limites aceitáveis. Se necessário, ajuste o ambiente ou aguarde até que as condições sejam adequadas.
3. Não Realizar a Manutenção Preventiva
A falta de manutenção preventiva nos equipamentos pode levar a erros durante a calibração. Instrumentos que não são mantidos adequadamente podem apresentar desgastes, sujeira ou danos que afetam suas medições. Para evitar esse erro, implemente um programa de manutenção regular para todos os equipamentos. Isso inclui limpeza, inspeção e reparos conforme necessário. A manutenção em autoclave hospitalar é um exemplo de como a manutenção regular é crucial para garantir a eficácia dos processos de esterilização e a precisão das medições.
4. Uso de Padrões de Referência Inadequados
Outro erro comum é a utilização de padrões de referência inadequados ou não calibrados. Para garantir a precisão da calibração, é essencial utilizar padrões que sejam rastreáveis a padrões nacionais ou internacionais. Além disso, os padrões de referência devem ser calibrados regularmente para garantir sua precisão. Para evitar esse erro, sempre verifique a validade e a rastreabilidade dos padrões de referência que você está utilizando. Se necessário, realize a calibração dos padrões antes de usá-los.
5. Documentação Inadequada
A documentação é uma parte vital do processo de calibração, mas muitas vezes é negligenciada. A falta de registros precisos pode levar a confusões e erros futuros. Para evitar esse problema, mantenha registros detalhados de todas as calibrações realizadas, incluindo as medições iniciais, os ajustes feitos e as medições finais. A documentação deve ser clara e organizada, permitindo que outros profissionais compreendam o processo realizado. Além disso, mantenha um histórico de calibrações para facilitar auditorias e revisões.
6. Falta de Treinamento da Equipe
A calibração é um processo técnico que requer conhecimento e habilidades específicas. Um erro comum é a falta de treinamento adequado da equipe responsável pela calibração. Profissionais não treinados podem cometer erros que comprometem a precisão das medições. Para evitar esse problema, invista em treinamentos regulares para sua equipe. Isso inclui a compreensão dos procedimentos de calibração, o uso correto dos equipamentos e a interpretação dos resultados. Um time bem treinado é fundamental para garantir a qualidade do processo de calibração.
7. Não Realizar Recalibrações Regulares
Após a calibração inicial, muitos profissionais cometem o erro de não estabelecer um cronograma de recalibração. A calibração não é um evento único; é um processo contínuo que deve ser realizado regularmente. Para evitar esse erro, crie um cronograma de recalibração com base nas recomendações do fabricante e nas condições de uso do equipamento. Equipamentos que são utilizados com frequência ou que estão sujeitos a condições adversas podem exigir calibrações mais frequentes.
Em resumo, a calibração é um processo essencial que deve ser realizado com atenção e rigor. Evitar os erros comuns mencionados acima garantirá que seus instrumentos de medição funcionem corretamente e forneçam resultados precisos. A implementação de um planejamento adequado, a manutenção preventiva, o uso de padrões de referência adequados, a documentação precisa, o treinamento da equipe e a realização de recalibrações regulares são práticas fundamentais para garantir a eficácia do processo de calibração. Ao seguir essas diretrizes, você estará contribuindo para a qualidade e a confiabilidade dos dados coletados em sua organização.
Frequência Ideal de Calibração para Diferentes Equipamentos
A calibração é um processo essencial para garantir a precisão e a confiabilidade dos instrumentos de medição. No entanto, a frequência com que a calibração deve ser realizada pode variar significativamente de acordo com o tipo de equipamento, sua aplicação e as condições em que é utilizado. Neste artigo, discutiremos a frequência ideal de calibração para diferentes equipamentos, ajudando você a entender melhor como manter seus instrumentos em conformidade e funcionando corretamente.
1. Equipamentos de Laboratório
Os equipamentos de laboratório, como balanças, pipetas e espectrofotômetros, são frequentemente utilizados em ambientes onde a precisão é crucial. A calibração desses instrumentos deve ser realizada regularmente, geralmente a cada três a seis meses, dependendo da frequência de uso e da criticidade das medições. Em laboratórios que realizam testes de alta precisão, como os farmacêuticos, a calibração pode ser necessária mensalmente. Além disso, sempre que um equipamento for movido ou submetido a condições adversas, uma nova calibração deve ser realizada.
2. Equipamentos de Medição Industrial
Em ambientes industriais, a calibração de instrumentos como manômetros, termômetros e sensores de pressão é igualmente importante. A frequência de calibração para esses equipamentos pode variar de seis meses a um ano, dependendo do tipo de equipamento e das condições de operação. Equipamentos que operam em ambientes agressivos ou que estão sujeitos a vibrações e choques podem exigir calibrações mais frequentes. É fundamental seguir as recomendações do fabricante e realizar uma avaliação periódica das condições de uso para determinar a necessidade de recalibração.
3. Equipamentos de Saúde
No setor de saúde, a calibração de equipamentos médicos, como monitores de pressão arterial, termômetros e autoclaves, é vital para garantir a segurança dos pacientes. A frequência de calibração para esses dispositivos pode variar, mas geralmente é recomendada a cada seis meses a um ano. No caso de autoclaves, a manutenção de autoclave odontológica deve incluir a calibração regular dos sensores de temperatura e pressão para garantir a eficácia dos ciclos de esterilização. Além disso, sempre que um equipamento apresentar falhas ou for submetido a manutenção, uma nova calibração deve ser realizada.
4. Equipamentos de Medição de Campo
Equipamentos de medição de campo, como medidores de pH, medidores de umidade e termômetros de infravermelho, também requerem calibração regular. A frequência ideal para esses instrumentos pode variar de três a doze meses, dependendo do tipo de medição e das condições ambientais. Por exemplo, medidores de pH utilizados em ambientes químicos agressivos podem exigir calibrações mais frequentes, enquanto termômetros de infravermelho usados em condições estáveis podem ser calibrados anualmente.
5. Equipamentos de Teste e Inspeção
Equipamentos utilizados para testes e inspeções, como câmeras termográficas e analisadores de qualidade do ar, devem ser calibrados regularmente para garantir a precisão dos resultados. A frequência de calibração para esses dispositivos pode variar de seis meses a um ano, dependendo da aplicação e do uso. É importante seguir as diretrizes do fabricante e realizar uma avaliação contínua das condições de operação para determinar a necessidade de recalibração.
6. Considerações Finais
A frequência ideal de calibração para diferentes equipamentos depende de vários fatores, incluindo o tipo de equipamento, a criticidade das medições e as condições de uso. É fundamental seguir as recomendações do fabricante e implementar um cronograma de calibração que atenda às necessidades específicas de sua operação. Além disso, a realização de manutenções preventivas e a documentação adequada das calibrações realizadas são práticas essenciais para garantir a precisão e a confiabilidade dos instrumentos.
Em resumo, a calibração é um processo contínuo que deve ser adaptado às necessidades de cada equipamento e ambiente. Ao entender a frequência ideal de calibração para diferentes instrumentos, você pode garantir que seus equipamentos estejam sempre funcionando corretamente, proporcionando medições precisas e confiáveis. Isso não apenas melhora a qualidade dos resultados, mas também contribui para a segurança e a eficiência das operações em sua organização.
Em conclusão, a calibração é uma prática essencial que não deve ser negligenciada em qualquer setor que dependa de medições precisas. Através da calibração regular, é possível garantir a qualidade dos produtos e serviços, além de assegurar a segurança das operações. Ao seguir os passos adequados para a calibração, evitar erros comuns e estabelecer uma frequência ideal para cada tipo de equipamento, as organizações podem otimizar seus processos e minimizar riscos. Investir na calibração não é apenas uma questão de conformidade, mas uma estratégia inteligente para promover a eficiência e a confiabilidade em todas as operações.